隨著國產(chǎn)大飛機、高鐵等大國重器快速崛起,人們也越來越發(fā)現(xiàn)材料領(lǐng)域的極端重要性。近日,在第五屆中國工業(yè)大獎發(fā)布會上,中國建材集團旗下巨石集團有限公司、蚌埠玻璃工業(yè)設(shè)計研究院有限公司兩家企業(yè)獲中國工業(yè)大獎。至此,中國建材集團旗下企業(yè)已基于玻璃纖維、超薄觸控玻璃、石膏板三項實現(xiàn)工業(yè)化量產(chǎn)的產(chǎn)品,摘得三個工業(yè)領(lǐng)域最高獎項。
中國工業(yè)大獎企業(yè):巨石集團
中國玻纖業(yè)從引進技術(shù)到自主設(shè)計
玻璃纖維是一種新型無機非金屬材料,能替代鋼材、木材、石材、鋁材等傳統(tǒng)材料,是國家戰(zhàn)略性新興產(chǎn)業(yè)之一。玻璃纖維之于新材料,就如水泥之于鋼筋,起到骨架支撐作用,在國防軍工、航空航天、交通運輸、節(jié)能環(huán)保、電子電器等領(lǐng)域均有廣泛應(yīng)用。沒有玻璃纖維,大飛機、高鐵、汽車等交通工具會變得非常笨重,風(fēng)力發(fā)電機組無法高高聳立,森林、礦產(chǎn)等資源的消耗速度大大加快,手機、電腦、家用電器等產(chǎn)品的電子線路板就沒法生產(chǎn),也就沒有信息技術(shù)的高速發(fā)展和人類社會的便捷高效。
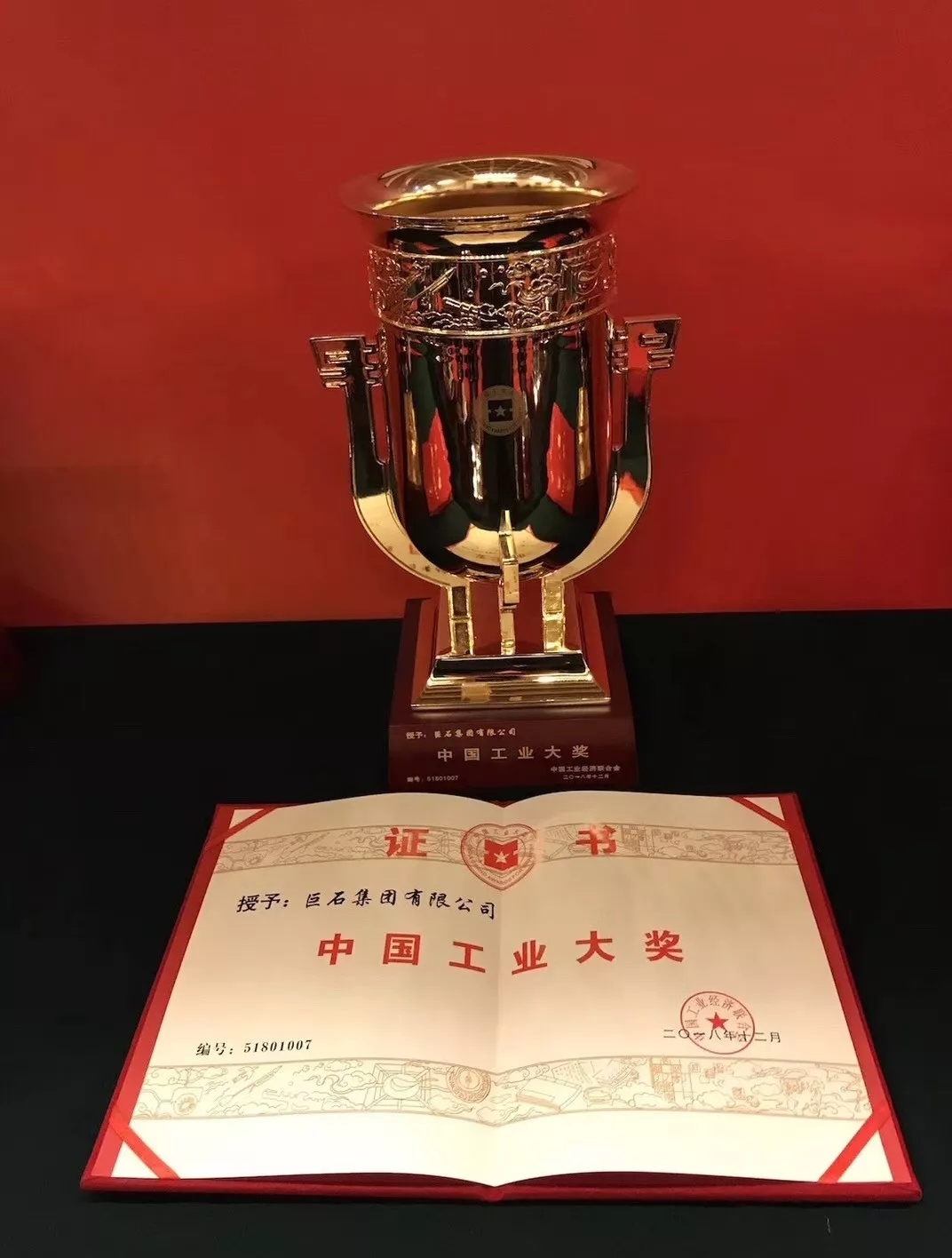
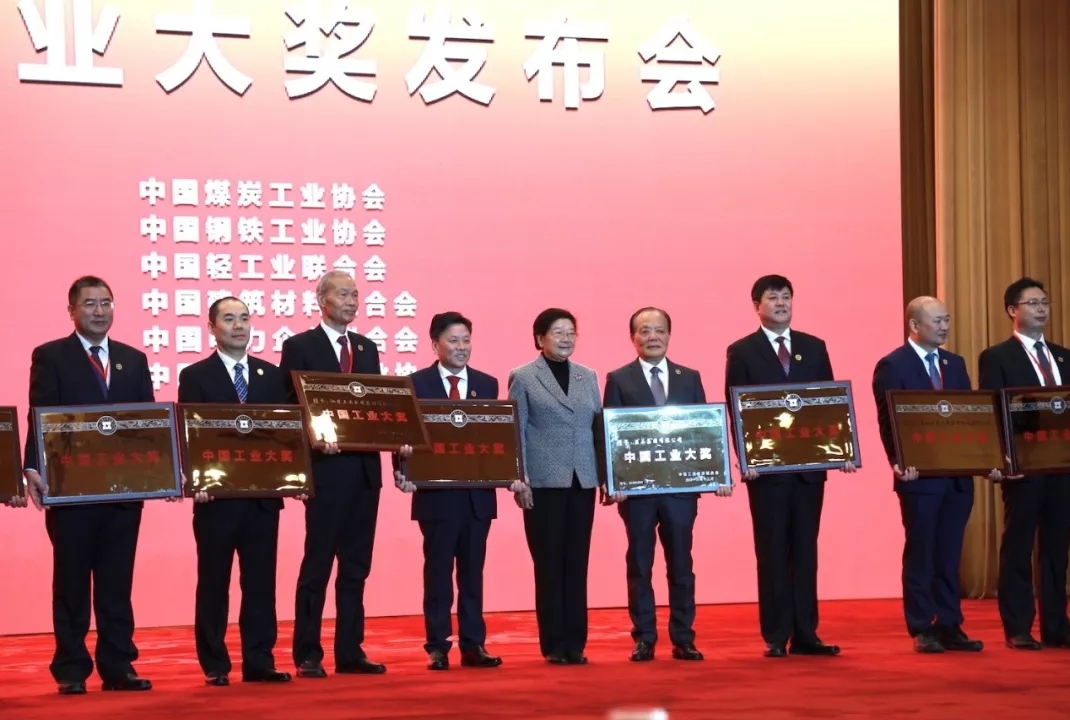
中國巨石總裁、巨石集團董事長兼CEO張毓強現(xiàn)場領(lǐng)獎,并作為獲獎企業(yè)代表上臺發(fā)言
玻璃纖維最早誕生于1938年的美國,并于1958年傳入我國,但由于歐美發(fā)達國家長期對我國進行嚴(yán)格的技術(shù)封鎖,直到上世紀(jì)90年代初,我國玻纖工業(yè)仍未擺脫一窮二白的落后面貌,與國際最先進的生產(chǎn)技術(shù)相比落后了50年。1993年,中國建材所屬中國巨石開始嘗試玻璃纖維的池窯化生產(chǎn),自主設(shè)計建設(shè)了中國首座大型池窯拉絲生產(chǎn)線,與發(fā)達國家之間的差距縮短到30年左右。
從1993年至2018年,這25年來,中國的玻璃纖維產(chǎn)業(yè)從弱到強,產(chǎn)能增長了30倍,產(chǎn)品性能提升50%,生產(chǎn)成本下降50%,玻纖年使用量從15萬噸增長至300萬噸,終端產(chǎn)品從約5000種拓寬至約50000種。中國玻纖工業(yè)擺脫了對國外的依賴,滿足了國民經(jīng)濟發(fā)展日益增長的需求,我國也成為全球最大的玻纖制造國和出口國。
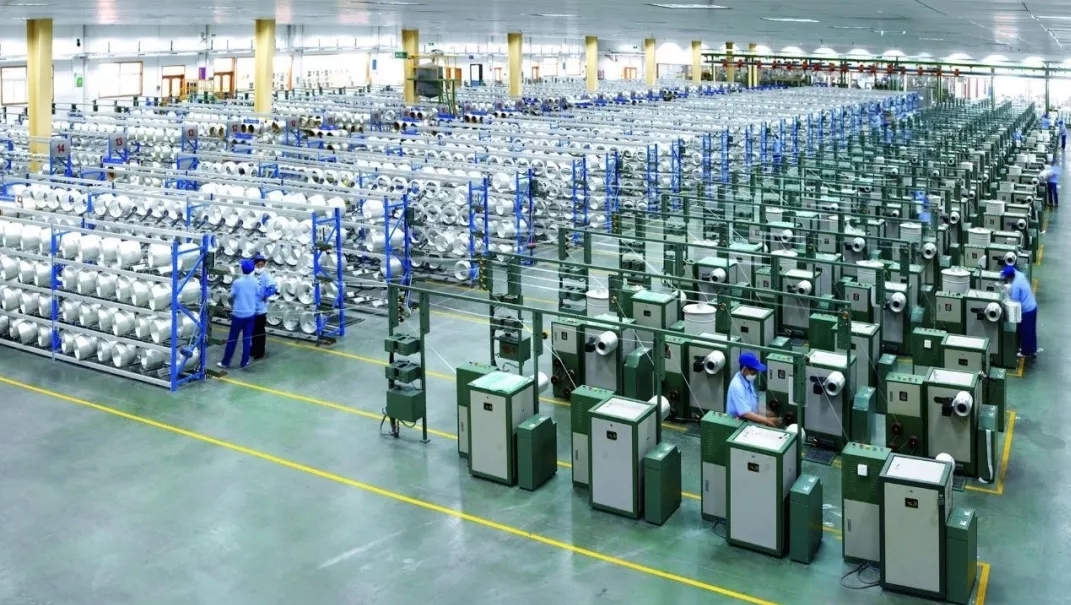
桐鄉(xiāng)生產(chǎn)基地絡(luò)紗車間
從國外壟斷到自主研發(fā)
2005年開始,中國巨石著手研發(fā)玻璃配方,直到2008年,成功研發(fā)E6配方。如今該配方的各項性能與國際巨頭的玻璃配方比肩,也成為中國玻纖企業(yè)中第一個獲得美國發(fā)明專利授權(quán)的配方,打破了美國在該技術(shù)上壟斷了70年的局面。目前巨石已經(jīng)擁有有效專利560件,其中發(fā)明專利121項,包括國外發(fā)明專利17項,保有量居國內(nèi)行業(yè)第一,構(gòu)建了核心技術(shù)專利池,以發(fā)明專利和國際專利為重點,近二年共申請國際發(fā)明專利近200件,取得授權(quán)17件。
2018年8月,中國巨石建成了全球唯一、規(guī)模最大的第一條智能生產(chǎn)線。目前該生產(chǎn)線各項運行數(shù)據(jù)均符合預(yù)期,并明顯領(lǐng)先于傳統(tǒng)生產(chǎn)線。比如,傳統(tǒng)生產(chǎn)線在窯爐點火后要1個月時間才能逐步達產(chǎn)達標(biāo),而該生產(chǎn)線僅用3天時間就實現(xiàn)達產(chǎn)達標(biāo)。
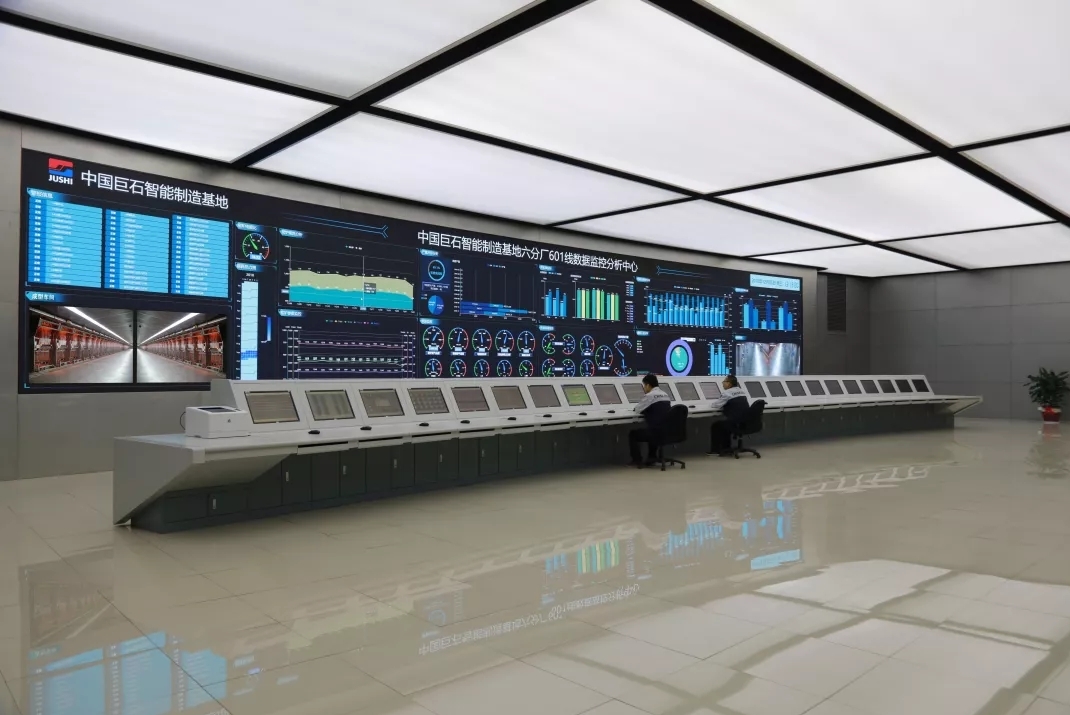
智能制造基地15萬噸生產(chǎn)線總控室
從扎根本土到走向世界
2009年12月,歐盟對中國出口的玻璃纖維發(fā)起反傾銷、反補貼調(diào)查,最終對中國巨石加征的稅率高達31.8%。被逼上梁山后,中國巨石經(jīng)過多方調(diào)研、分析、論證,最終選擇在埃及投資建廠,并取得極大成功。
如果說在埃及建廠是“有病治病”,那么在美國建廠則是“沒病防病”,事實證明,這個決策是正確的,由于提前進行海外布局,本次中美貿(mào)易摩擦對中國巨石的影響并不大。
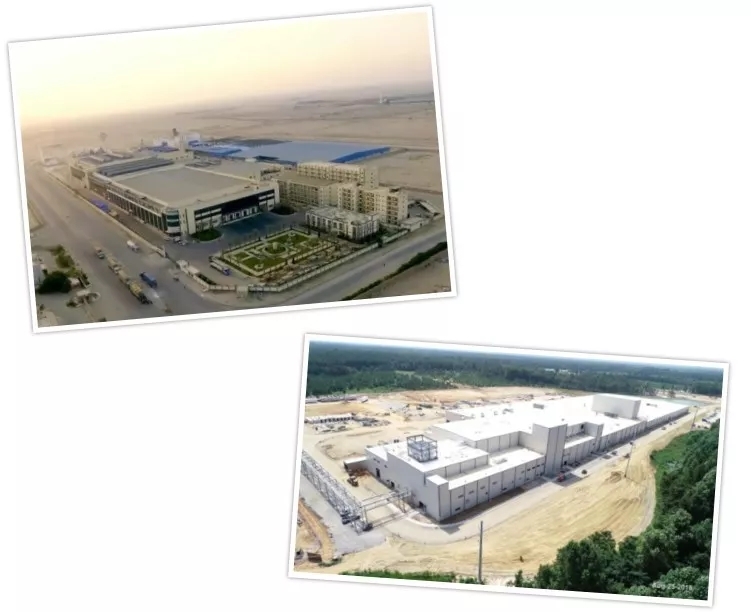
左上:中國巨石埃及20萬噸生產(chǎn)基地
右下:中國巨石美國8萬噸生產(chǎn)基地
經(jīng)過25年的發(fā)展,中國巨石成為了全球玻纖行業(yè)的單項冠軍,目前玻纖總產(chǎn)能160萬噸,占世界總產(chǎn)能的22%。其自主研發(fā)的高性能玻璃纖維,在產(chǎn)品質(zhì)量和制造技術(shù)上達到國際領(lǐng)先水平,得到諸多世界500強客戶的青睞。
中國工業(yè)大獎項目獎:蚌埠院超薄觸控玻璃關(guān)鍵技術(shù)與成套裝備開發(fā)及產(chǎn)業(yè)化
電子信息顯示產(chǎn)業(yè)是我國重要的支柱產(chǎn)業(yè)之一,但是電子信息顯示的核心部件曾100%依賴進口,一度成為我國僅次于芯片、石油、鐵礦石的第四大單一進口產(chǎn)品,并且占這一核心部件成本約30%的關(guān)鍵基礎(chǔ)材料——超薄信息顯示玻璃長期被國外壟斷,致使中國電子信息顯示產(chǎn)業(yè)關(guān)鍵環(huán)節(jié)缺失,產(chǎn)業(yè)規(guī)模受到嚴(yán)重制約,電子信息顯示產(chǎn)品價格長期居高不下。
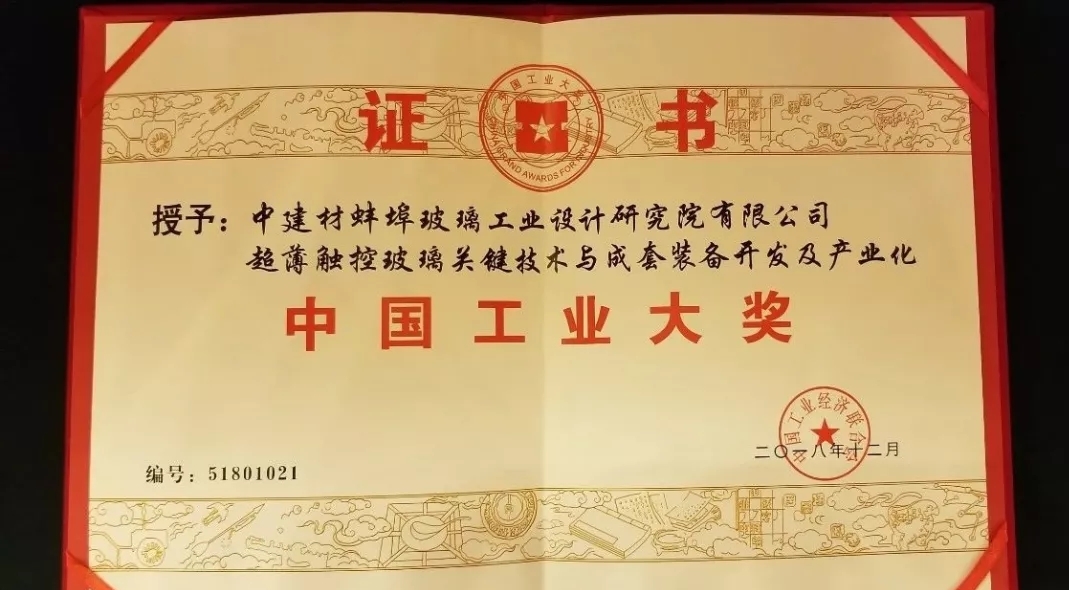
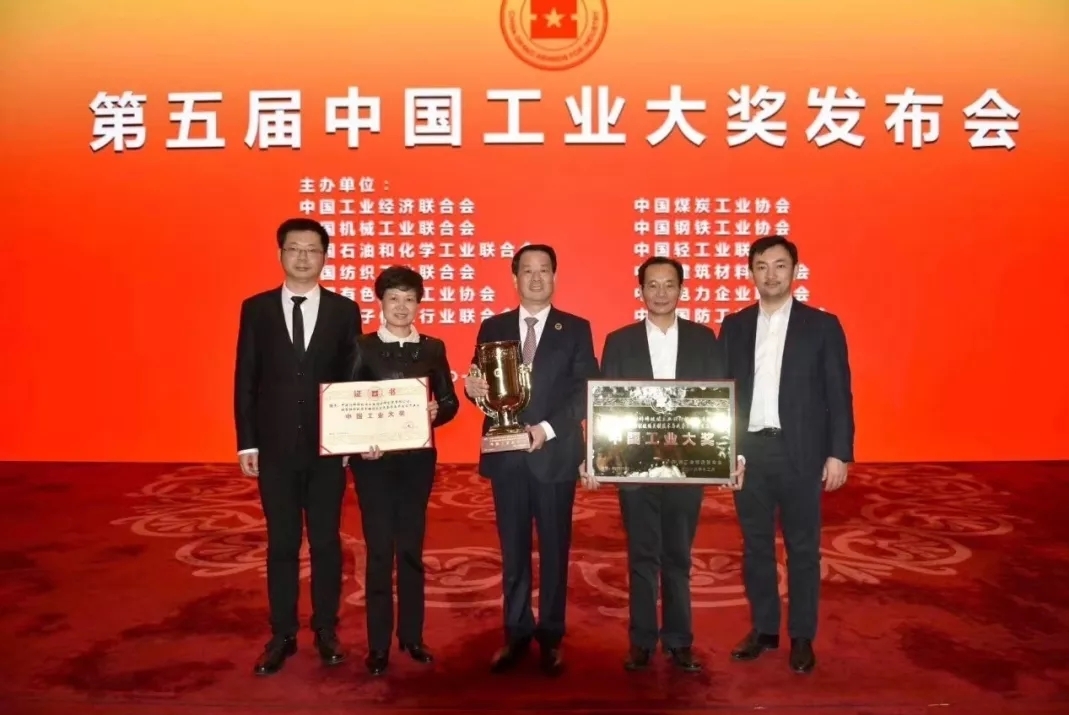
蚌埠院院長、浮法玻璃新技術(shù)國家重點實驗室主任彭壽作為項目獲獎代表領(lǐng)獎
超薄觸控玻璃作為超薄信息顯示玻璃的重要組成部分,目前國內(nèi)年需求量約1億平方米,市場前景廣闊。但其工藝技術(shù)復(fù)雜,需要多學(xué)科、多技術(shù)的高度復(fù)合集成,生產(chǎn)難度較大。
針對上述現(xiàn)狀,我們從上世紀(jì)90年代起開展原料提純、玻璃成分及配方、新型熔化、超薄成形、精深加工等關(guān)鍵核心技術(shù)與裝備的科技攻關(guān),形成了我國具有自主知識產(chǎn)權(quán)的超薄觸控玻璃工業(yè)化制備核心技術(shù)及成套裝備,成功實現(xiàn)產(chǎn)業(yè)化,建成國內(nèi)唯一一條穩(wěn)定量產(chǎn)世界最薄0.12毫米超薄觸控玻璃智能化生產(chǎn)線,使我國在該領(lǐng)域達到世界領(lǐng)先水平。該成套技術(shù)在臺玻、南玻等知名企業(yè)成功推廣應(yīng)用。本項目的實施,打破了國外技術(shù)封鎖與市場壟斷,填補了電子信息顯示產(chǎn)業(yè)鏈關(guān)鍵環(huán)節(jié)缺失,為國家電子信息顯示產(chǎn)業(yè)安全做出了重要貢獻。
作為電子信息顯示產(chǎn)業(yè)的核心材料,超薄觸控玻璃,可用來做手機、電腦、電視顯示屏基礎(chǔ)材料。未來攻關(guān)計劃柔性化,超薄觸控玻璃向0.1毫米以下發(fā)展,以適應(yīng)未來柔性顯示產(chǎn)業(yè)的發(fā)展,為曲面顯示,可穿戴設(shè)備研制和生產(chǎn),基礎(chǔ)材料打下了良好的基板原料基礎(chǔ)。
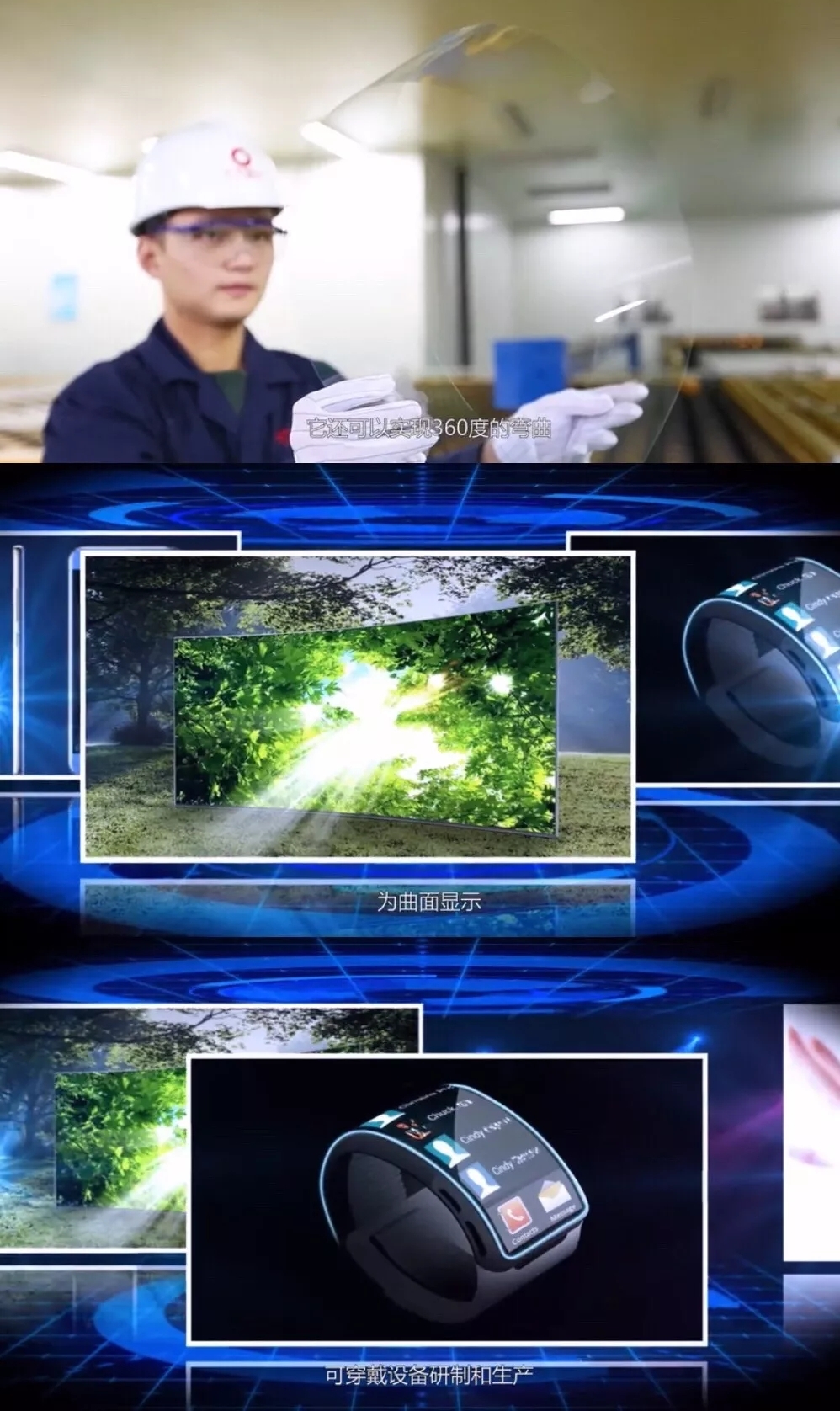
蚌埠院近年來通過改革科研體制、強化激勵措施、打造創(chuàng)新平臺,使資本、人才、技術(shù)充分融合,在電子玻璃高端化升級方面每年向前跨越一大步,為民族玻璃工業(yè)的快速發(fā)展提供了新的動能。
2014年、2015年、2016年,0.3毫米、0.2毫米、0.15毫米,每年一個臺階,2018年4月,歷經(jīng)2年時間,蚌埠院又成功生產(chǎn)0.12毫米極薄玻璃。超薄觸控玻璃厚度每下降0.1毫米,甚至0.01毫米,都需要對熔化、成型、退火、切裁、檢驗包裝工藝技術(shù)和核心裝備等進行全方位的創(chuàng)新。
超薄觸控玻璃從0.33毫米到0.2毫米,從0.2毫米到0.15毫米,從0.15毫米到0.12毫米,是200多名科研人員和凱盛工匠,經(jīng)歷無數(shù)個日夜攻關(guān),突破1000多項關(guān)鍵技術(shù)瓶頸,用辛勞和汗水換來的碩果。
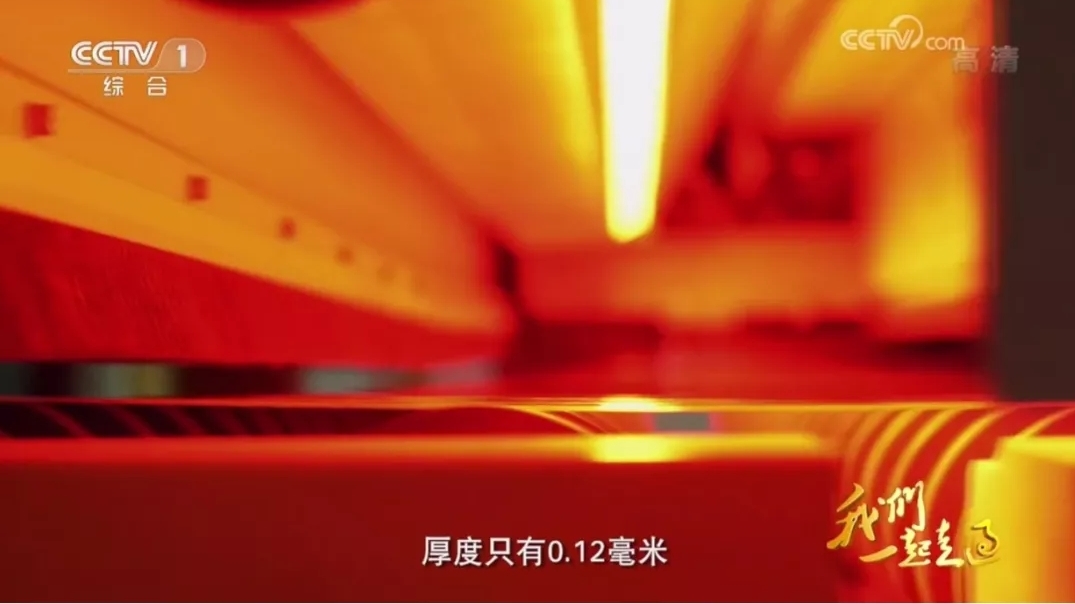
超薄觸控玻璃研發(fā)攻堅和工程建設(shè)成為了中國創(chuàng)造和中國制造的“凱盛加速度”。0.12毫米玻璃的問世,不僅打破了蚌埠院2016年創(chuàng)造的0.15毫米國內(nèi)電子玻璃工業(yè)化生產(chǎn)極限,而且又一次刷新了中國超薄電子玻璃薄型化的生產(chǎn)紀(jì)錄,再次填補國內(nèi)空白。與此同時,每年還將為我國電子信息顯示產(chǎn)業(yè)降低成本約120億元,為國家節(jié)約外匯約20億美元。
正是這塊玻璃,助力華為、小米等國產(chǎn)品牌騰飛,使人民大眾直接受惠于民族產(chǎn)業(yè)的崛起,對增強國家綜合實力,保障國家電子信息顯示產(chǎn)業(yè)安全作出了重要貢獻。 該文觀點僅代表作者本人,如有文章來源系網(wǎng)絡(luò)轉(zhuǎn)載,本網(wǎng)系信息發(fā)布平臺,如有侵權(quán),請聯(lián)系本網(wǎng)及時刪除。
|